Further evaluation made by the Joint Investigation Team week commencing the 6th of February 2017
A further site visit was conducted for the remainder of the joint investigation team who could get access to Sabetta in January.
No further failure mechanismswere reported by the joint investigation team. Samples were taken to evaluate the root cause of the cracking. The following samples were taken from the structures:
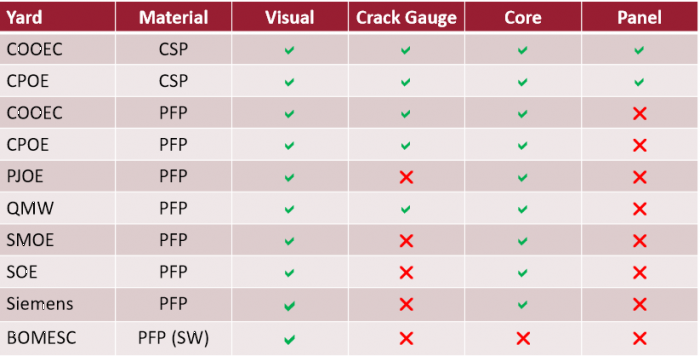
The following analysis is to be undertaken by the joint investigation team:
§ To carry out visual survey of defective areas
§ To select representative samples for chemical & physical testing
§ 3cm Ø & 8cm Ø core samples for
§ FTIR (Fourier Transformation Infra Red)
§ DSC (Differential Scanning Calorimetry)
§ TGA ( Thermal Gravimetry Analyiss)
§ SEM fractography (Scanning Electron Microscopy)
§ 25cm x 25cm panel sample
§ DBTT (Design Brittle Transition Temperature)
§ To fit strain gauges for monitoring crack development in live cracks
§ To commence root cause analysis
The temperature at Sabetta was lower than for the initial investigation (-35C as oppose to -20C in January). Cracks were reported to still be propagating in some areas whereas for others the crack propagation had ceased.
For the passive fire protection,
The situation for the Defect type A was essentially similar to the observations in January. Some of the beams exhibited cracking on the flanges as well as the web which were not observable in January. However the majority of the defects were still apparent on the webs of the beams.
A greater number of fine cracks were observable on small beams (Defect type B) between the flange and web interface.
For the cold spill protection system,
The maximum width of the cracks had increased to 5mm due to further shrinkage upon cooling with respect to the steel work. It would be expected that when temperatures increased the crack width at the temperatures observed in January would be similar. The material shows no sign of falling off the steel which consistent with the observations in January.
It was confirmed that there is a requirement to reinstate the PFP and CSP protection for the MCHE.
Repair Proposals
Initial thoughts on repair options for passive fire protection and cold spill protection were sent at an earlier date for comment after the visit to site in January (Appendix 2)
These were not formally circulated at the wrap up meeting in February by the joint investigation team. Development of the repair procedure will occur week commencing the 13th of February following face to face meetings and feedback from the fabricators responsible for the application of the cold spill protection systems and passive fire protection systems for Yamal LNG.